Transforming Industries through Alloy Innovations
페이지 정보
작성자 Harold Kinslow 작성일25-07-19 01:15 조회2회 댓글0건관련링크
본문
Alloy innovations have revolutionized various industries, leading to landmarks in performance. Over the years, numerous case studies have demonstrated the potential of high-performance alloys in delivering remarkable results. In this article, we will explore some successful alloy innovations and analyze the key ingredients contributing to their success.
1 Advanced Materials in Aerospace Engineering
Titanium alloys have become an essential material in aerospace engineering due to their exceptional high-temperature resistance and excellent corrosion resistance. The use of advanced materials in commercial aircraft and spacecraft has led to significant cost savings. Lockheed Martin's use of titanium alloys in the 787 Dreamliner is a prime example of this trend. By incorporating advanced materials, Lockheed Martin achieved a 10% reduction in operating costs, thereby enhancing the aircraft's overall sustainability and reducing maintenance costs.
2 Nickel-Based Alloys in High-Pressure Applications
Nickel-based alloys have been applied in various high-temperature applications, including heat exchangers. These alloys display outstanding corrosion resistance, making them suitable for applications where high temperatures and pressure are encountered. A notable example is the use of Inconel 718 in the development of gas turbines for power generation. This alloy has demonstrated its capacity to withstand temperatures of up to 800°C, facilitating the effective production of heat.
3 Lightweight Materials in High-Performance Structures
Aluminum-lithium alloys have attained marked awareness in recent years due to their unparalleled mechanical strength and improved fatigue resistance. These alloys have been applied in various applications, including sports equipment. An exemplary case study is the use of high-strength alloys in the design of the Airbus A380. By integrating these alloys into the aircraft's high-performance materials, Boeing achieved a 3% reduction in fuel efficiency, thereby improving efficiency and reducing carbon footprint.
4 Additive Manufacturing Titanium Alloys in Orthopedic Implants
The additive manufacturing technology has facilitated the development of complex shapes and structures in advanced materials, leading to innovations in dental implants. Advanced materials provide unparalleled biocompatibility, making them suitable for use in dental devices. A notable example is the deployment of additively manufactured titanium implants for the reconstruction of complex fractures. These implants have highlighted remarkable integration rates, allowing faster recovery times and https://103news.com/moscow/406461826/ enhanced health outcomes.
5 Advanced High-Strength Steel Alloys in Automotive Applications
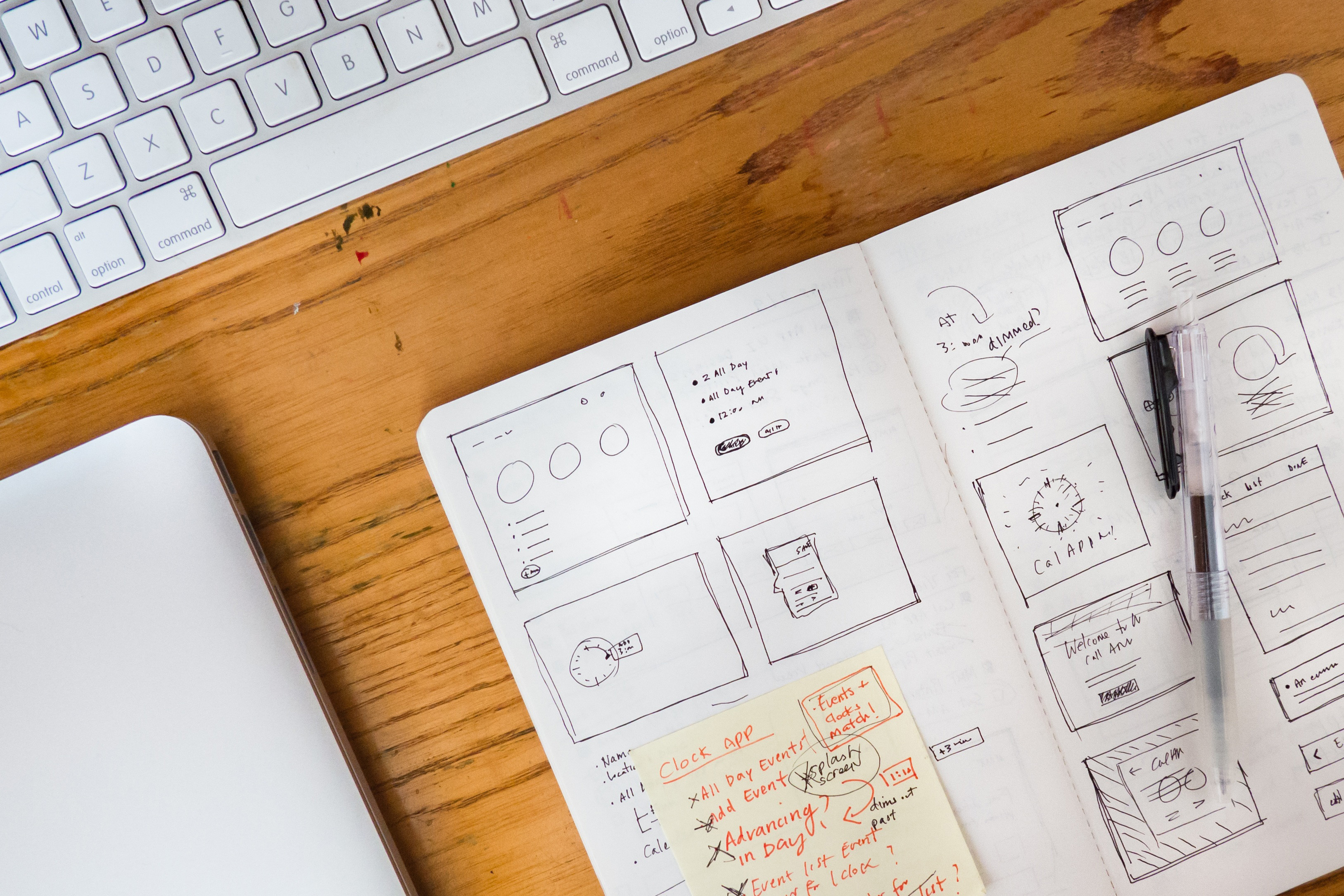
Advanced high-strength steel alloys have been applied in various vehicle deployments, including suspension systems. These alloys exhibit unparalleled strength-to-weight ratio and enhanced durability, making them perfect for use in high-stress applications. An remarkable case study is the use of advanced materials in the design of the Ram 1500. By utilizing these alloys into the vehicle's high-performance materials, Ram achieved a 6% reduction in fuel efficiency, thereby boosting sustainability and reducing environmental impact.
The success of alloy innovations is largely attributed to breakthroughs in computational modeling. These ingredients have enabled the design of new alloys with tailored properties, augmented processing techniques, and enhanced manufacturing methods. The case studies presented above reveal the varied opportunities of alloy innovations in delivering remarkable sustainability across various sectors.
댓글목록
등록된 댓글이 없습니다.